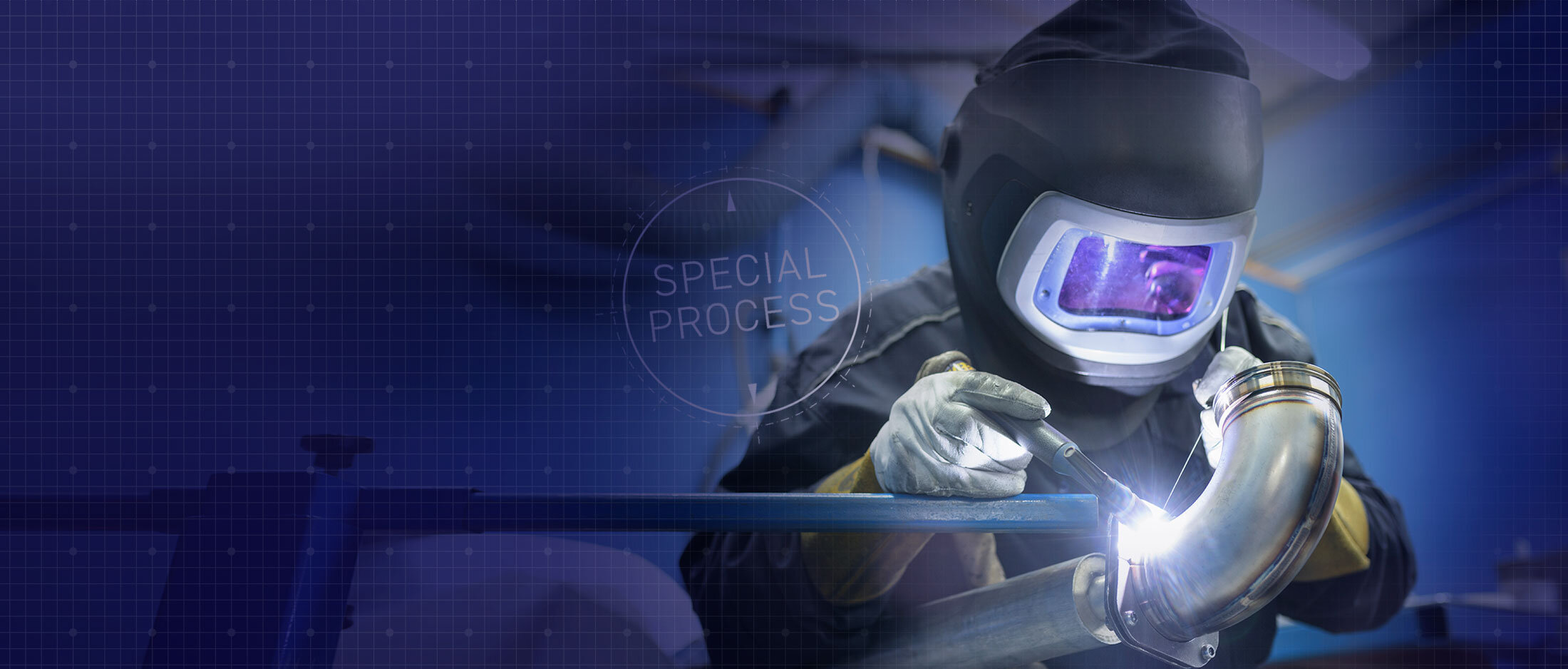
Special Processes
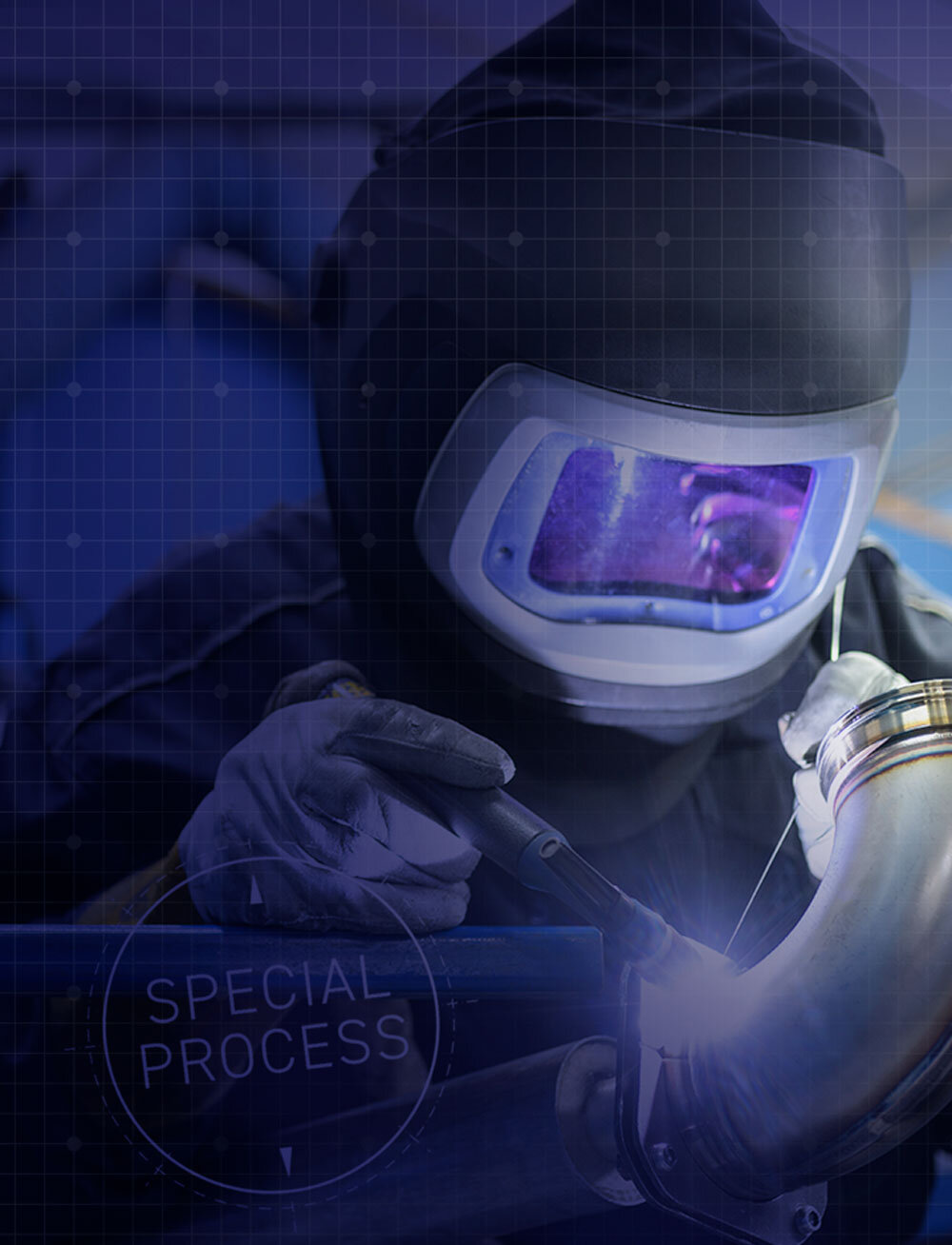
Special
Processes
Often, components and parts cannot be verified without destructive testing and therefore require a special process to confirm compliance. Being Nadcap accredited, we adhere to the highest quality special processes which are defined in the aerospace industry as…
“A set of linked procedures that lead to the creation of products and services whose end results would not otherwise be measured, monitored or verified before being released; therefore requiring special attention during production to ensure they are free of defects.”
Within RHH Franks, compliance with Nadcap defined checklists apply to all procedures that require it, regardless of sector.
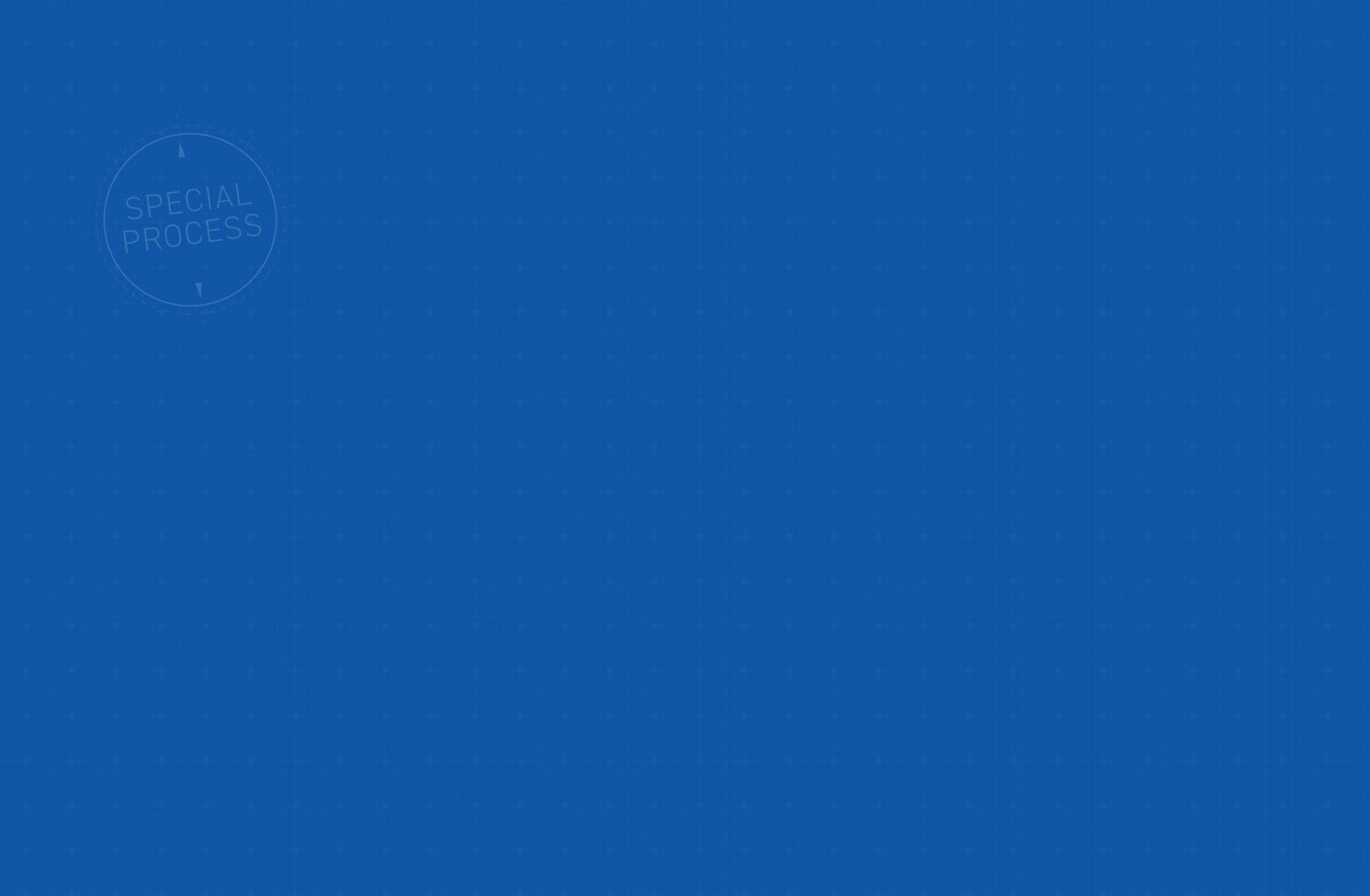
The special processes we undertake include:
Heat Treatment
Annealing, Solution Treating
Precipitation and Stress Relieving
Accredited February 2006
TIG Welding and Torch Brazing
Aluminium, Titanium, Stainless and Carbon Steels
CAA Coded Welders
Accredited November 2004
Dip Brazing
Two 24” Diameter Salt Baths
Pre-Heat Oven to AMS2750
Accredited February 2006
Penetrant Flaw Detection (PFD)
Water washable Level 2 Line
Post-emulsified Level 3 capability
Accredited March 2004
Paint Finishing
Painting and Dry Film Coatings
Post-Paint Testing
Accredited November 2009
In Action
An aerospace engine manufacturer had an existing solid casting part, which was notoriously expensive to manufacture, required a minimum order quantity from the foundry along with lengthy lead times. The client wanted a more cost-effective and accessible method of manufacture.
By reverse engineering the casting, we were able to design a specialist outer ring and internal fins along with a fixture to enable the part to be dip brazed to Nadcap special process standards. This significantly reduced the lead time and cost for the client.